- Kajima Corporation’s automated construction system operates 20 heavy machines autonomously at the Naruse Dam construction site in Higashinaruse, Akita Prefecture, Japan.
- The project signifies the world’s first fully automated dam construction, demonstrating Japan’s commitment to using AI and remote operations to address labor shortages.
- Remote operators, including a mother caring for her 3-year-old child, control the machines from a distance of up to 1,800 kilometers, showcasing the transformative potential of AI and automation in construction.
In the village of Higashinaruse, Akita Prefecture, Japan, an extraordinary development is underway: a dam construction site where 20 heavy machines operate autonomously, tirelessly working without a human in sight.
This project represents the world’s first fully automated dam construction endeavor, showcasing Japan’s commitment to leveraging AI and remote operations to address labor shortages.
Remarkably, employees situated 400 kilometers away in Kanagawa skillfully control these massive machines, demonstrating the transformative potential of AI and automation in the construction industry.
Even a mother, clad in slippers, can now operate an excavator located 1,800 kilometers away, all while caring for her child—a remarkable fusion of convenience and innovation in action.
Addressing labor shortages with automation
Japan’s construction industry has long grappled with labor shortages, particularly in remote areas where skilled workers are scarce. To overcome this challenge, Kajima Corporation, founded in 1840, one of the oldest and largest construction companies in Japan, has turned to automation, leveraging AI-driven technologies to operate heavy machinery remotely.
We have worked on pioneering projects across the generations, including the country’s first skyscraper and many different national development projects in areas such as social infrastructure. We are proud of the contributions we have made toward Japan’s economic and industrial development.
Hiromasa Amano, President and Representative Director Kajima Corporation
Hiromasa Amano, President and Representative Director of Kajima Corporation, has stated that the company has been involved in pioneering projects across different generations, including Japan’s first skyscraper and various national development initiatives focusing on social infrastructure. Amano expressed pride in the contributions made towards Japan’s economic and industrial development.
With just three programmers stationed 400 kilometers away in Kanagawa Prefecture, Kajima can control a fleet of 20 heavy machines tirelessly constructing the Naruse Dam.
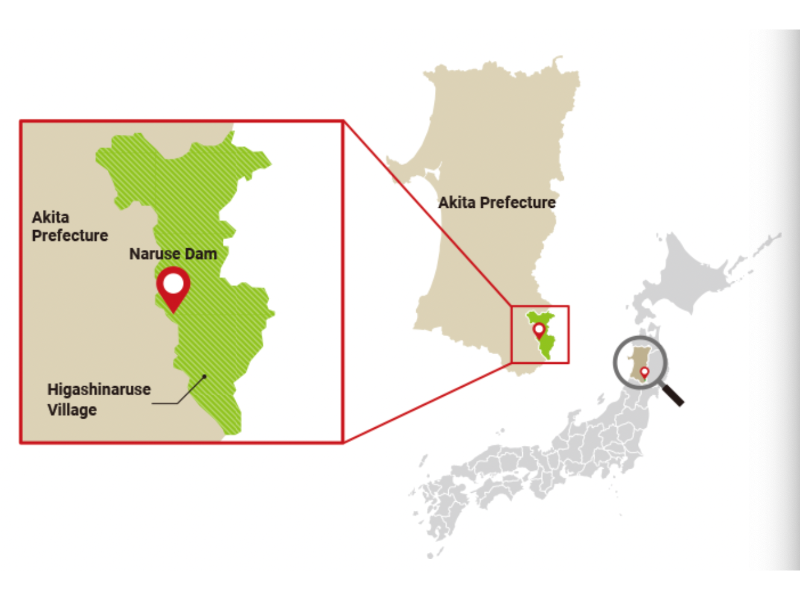
Enhanced efficiency and safety
The Naruse Dam construction site buzzes with activity as automated machines work day and night, except during refueling time, and during the peak construction season, 70 hours of continuous construction are scheduled. They are guided by precise algorithms and monitored by skilled engineers.
Unlike human laborers, these machines never tire, ensuring exceptional productivity while maintaining high quality. Moreover, by eliminating the need for human operators on-site, Kajima minimizes the risk of workplace accidents, enhancing overall safety.
Also read: The automation dilemma: Convenience or over-reliance?
The A4CSEL System: Powering the future of construction
At the heart of Kajima’s automated construction revolution lies the A4CSEL system, short for “Automated Construction with Computerized System for Enhanced Labor.” Developed in 2009, this advanced technology allows for the seamless coordination of multiple construction machines, optimizing productivity and efficiency. From bulldozers to dump trucks, each machine is meticulously controlled by the A4CSEL system, ensuring precise and synchronized operations.
Beyond construction sites, Kajima’s automated machinery opens new possibilities for remote operations in various sectors. In agriculture, mining, and beyond, the ability to control heavy machinery from afar revolutionizes traditional workflows. With remote operators able to manage equipment from hundreds of kilometers away, the potential for efficiency gains is immense.
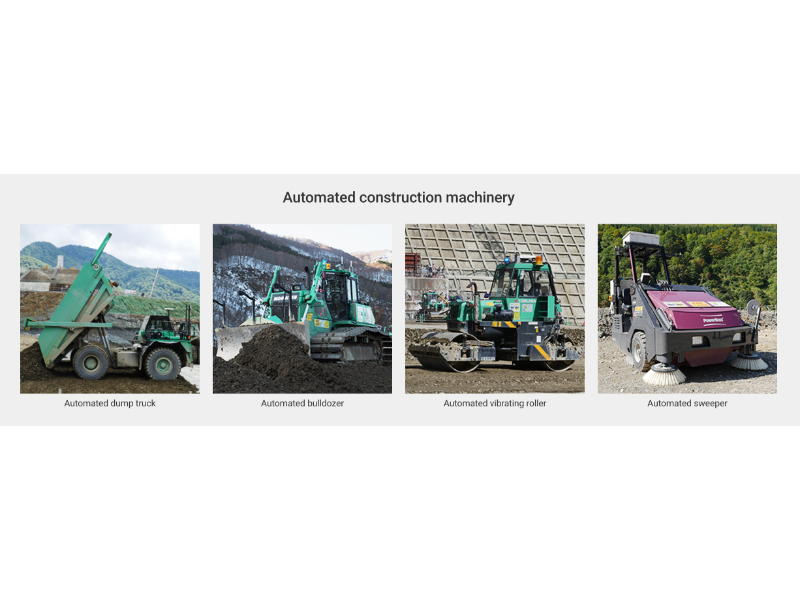
Transforming construction sites into factories
Through the implementation of the A4CSEL system, Kajima aims to transform traditional construction sites into high-tech factories.
At the Naruse Dam site, more than 20 automated construction machines work in unison, seamlessly unloading, spreading, and compacting embankment materials to construct the dam’s foundation. This innovative approach not only accelerates construction but also sets a new benchmark for quality and precision in dam building.
Pop quiz
What construction machines are automated?
A. dump truck
B. vibrating roller
C. bulldoser
D. sweeper
See the answer at the bottom of the article.
How AI and robotics play a part?
To maintain peak efficiency, Kajima has integrated AI and machine learning algorithms into its automated construction system. These algorithms learn from the operations of experienced workers, adapting and optimizing machine behavior to suit various construction scenarios.
As a result, Kajima’s automated construction machines operate with unparalleled efficiency, even in challenging conditions.
Picture this: a self-driving dump truck, devoid of any human presence, autonomously gliding toward the material loading area with laser-like accuracy, halting precisely at the designated spot, ready to catch the incoming construction materials.
But that’s not all—the truck subtly adjusts its body position, ensuring a perfectly balanced load.
Brace yourself for the astonishing part: these dump trucks can reverse autonomously, elegantly retreating at the same speed they would while moving forward, even accelerating on flat terrain during their backward dance. When descending slopes, they gracefully decelerate, preventing any material mishaps.
As they reach the unloading point, the trucks perform a synchronized maneuver, with the cargo bed tilting automatically to gently release the materials, before smoothly transitioning to unmanned bulldozers and other machines in a well-rehearsed ensemble.
The true potential of technology lies in its application to real-world scenarios, not in the buzz it generates in press releases and tech expos. For technology companies entrenched in the construction space, the path forward involves a recalibration of focus — a pivot from the current hype of AI and ML capabilities to one of tangible, problem-solving applications and proof points.
Joel Hutchines, Chief Product Officer at Slate Technologies
According to Joel Hutchines, for technology companies deeply involved in the construction industry, moving forward requires a shift in focus. Instead of solely emphasizing the hype surrounding AI and ML capabilities, the key is to prioritize practical, problem-solving applications and tangible evidence of their effectiveness.
Kajima has moved beyond theoretical discussions, showcasing real-world solutions that address specific challenges faced in the construction sector. By demonstrating how these technologies can bring concrete benefits and solve actual problems, the corporation has established credibility and driven meaningful impact within the industry.
Also read: 5 women that are changing the AI industry
Naruse Dam: A testbed for innovation

The Naruse Dam project serves as a testbed for Kajima’s innovative construction technologies. As Japan’s largest trapezoidal CSG dam, with an embankment volume of 4.85 million m3, it presents unique challenges and opportunities for automation. Challenges include integrating complex automation systems, and ensuring reliability and safety in remote operations.
By utilizing AI and remote technologies, companies can optimize resource utilization, reduce manual labor requirements, and accelerate project timelines.
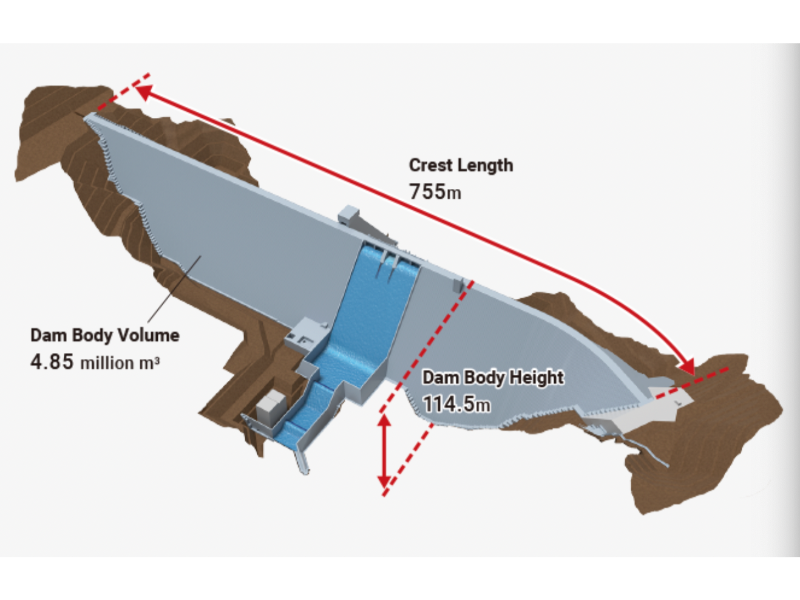
The dam will serve multiple functions, including disaster prevention, preservation of the river basin environment, maintenance and replenishment of tap water and agricultural irrigation water, hydroelectric power generation, and more. The dam will also contribute to the development and convenience of the surrounding area.
A4CSEL’s versatile application from earth to space
While initially developed for dam construction, Kajima’s automated construction technology holds promise for various other applications.
From dam, tunnel, to space exploration, the possibilities are vast. By commercializing this technology, Kajima aims to drive innovation across industries and shape the future of construction worldwide.
The application field of A4CSEL is not limited to Earth. Since 2016, A4CSEL has been collaborating with the Japan Aerospace Exploration Agency (JAXA) in a project that considers using A4CSEL in the construction of a manned base on the Moon. There may come a day in the not-too-distant future when A4CSEL will be active on the Moon.
Supporting workforce diversity and inclusion
Kajima’s automated construction system, also promotes workforce diversity and inclusion, taking the special need of female employees and injured staff into consideration.

Enter the Yamazaki Group in Japan’s Shimane Prefecture, a renowned name in civil engineering and demolition. Within their headquarters lies a room where a lone female worker, surrounded by seven monitors, skillfully manipulates control levers—a sight reminiscent of a flight simulator.
But here’s the twist: she’s not flying an aircraft. Instead, she remotely guides a hydraulic excavator positioned 100 meters away. Yes, you heard it right—no operator in the cab, yet the excavator responds with the finesse of a seasoned pro.
This excavator has nine strategically positioned cameras—on the cabin, the digging arm, and beyond. Ms. Ikuko, sporting Hello Kitty-branded sandals, directs the excavator’s actions by monitoring live video feeds from these cameras.
Now, let’s dive into the magic. Developed by construction machinery manufacturer Kobelco Construction Machinery two years ago, the system relies on high-speed communication lines linking the control room to the distant hydraulic excavator. It can also effortlessly switch between controlling multiple heavy machines. In a display, it even managed a hydraulic excavator situated 1,800 kilometers away in Hiroshima while being operated from Sapporo.
More surprisingly, Ms. Ikuko’s parenting challenges find a solution. When her 3-year-old son falls ill, she brings him to the room adjacent to the control center. There, the boy watches TV while she operates the excavator. It’s an ideal blend of remote work and nurturing—a scenario achievable only through remote control.
Meanwhile, the Yamazaki Group hopes that this system can provide an opportunity for the older generation of skilled workers to shine. For those who have fallen ill or experienced work injury, they don’t need to return to the construction site immediately after recovery; they can engage in remote operation while participating in rehabilitation efforts and even guiding new staff.
All these examples showcase the system’s capacity to accommodate diverse talents and circumstances, thereby contributing to a more inclusive and fair work environment.
Answer to the quiz: All of the 4 choices. A4CSEL has been successively applied to automate vibratory rollers, bulldozers, sweepers, and dump trucks onsite at several dam construction sites.